AMF Wheels Technology
AMF, its technology drives the evolution of sports wheels
What is AMF (Advanced Metal Forming)?
It is a type of rotational plasticity processing that rotates a metal pipe shaft and presses a roller against the raw material loaded there to shape it.
The image is the same as the potter's wheel and the clay attached to the potter's wheel.
This is the same principle as when a piece is gradually molded into an arbitrary shape by hand while rotating.
Casting and Forging
In general, the merits of casting are that aluminum alloy melted at high heat is poured into a mold, and the entire wheel is integrally molded, so there is a high degree of freedom in designing the disc surface, and mass production is easy, so the price is low and suppressed. On the other hand, from a technical point of view, it is difficult to make thin-walled molding, so there is a limit to weight reduction.
In addition, the aluminum structure formed by casting has many irregularities, and the ties of particles are weak, so it cannot be said to be strong.
Forged wheels, on the other hand, are formed by using a high-pressure press to form lumps of aluminum or alloy.
As a result, the aluminum particles are stretched and hardened along the shape of the wheel, creating strength (forging flow: metal flow).
Furthermore, due to the nature of the manufacturing method, forged wheels can be made lighter. At first glance, forging seems to be all good, but it has a decisive weakness, "The degree of freedom in design is not very high." As I mentioned earlier, forging is done by "crushing" with a press machine, so so-called wraparound or overlapping shapes are generally considered impossible.
Forging also has the disadvantage of being costly because it goes through several manufacturing processes.
Birth of the "third manufacturing method" to compensate for weaknesses
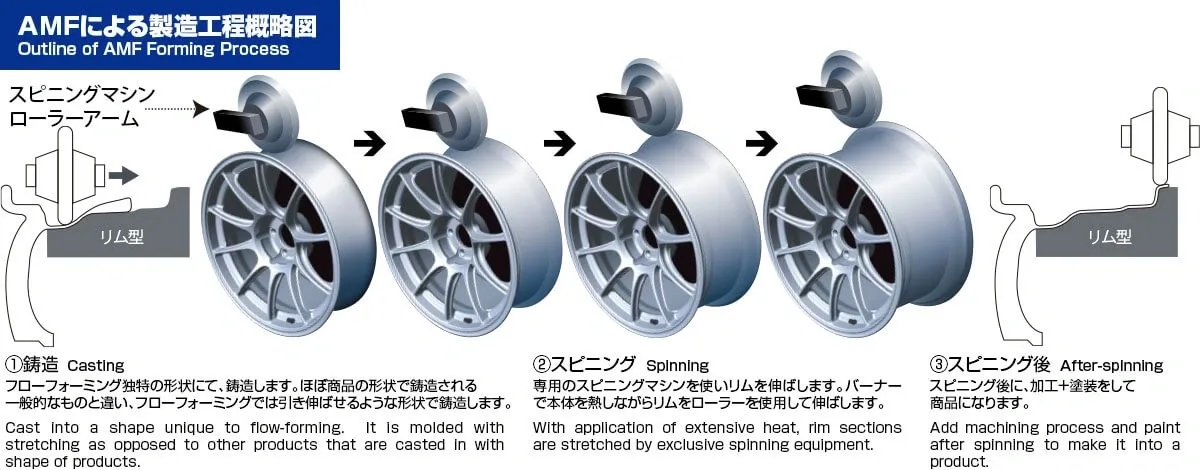
AMF first casts the disc face and then the shaped rim section. Then, the cast disk = rim material is put on a wheel-spinning machine to roll the rim.
This process further refines the crystals and macrostructures of the aluminum material, which increases toughness (flexibility) and achieves tenacious strength. As a result, a high-rigidity rim is born that has all the basic performances required for aluminum wheels, such as "tensile strength," "proof strength," and "elongation." In addition, compared to the conventional type of welding plate material into a ring, it has become possible to create a seamless tube rim with high precision.
Since the AMF disc surface is a conventional casting mold, the rim part is stretched to the minimum necessary thinness by a spinning machine while maintaining the freedom of design, making it extremely lightweight and reducing the unstrung load contribute. The third manufacturing method, which combines the merits of both casting and forging, is the so-called "AMF" (Advanced Metal Forming) spinning method. The AMF was born to realize the WedsSport brand concept of "faster and safer." A new generation of technology that has been trained in motorsports will appear with amazing performance.
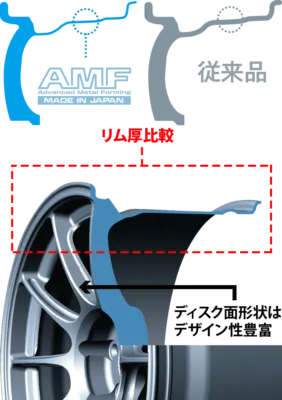
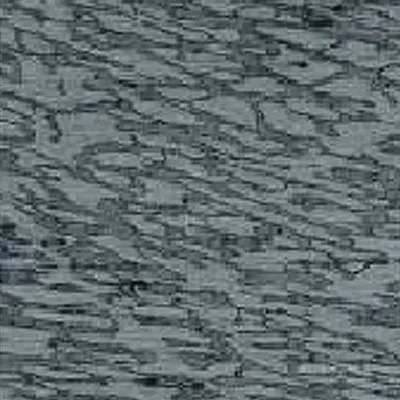
Aluminum structuredensified by AMF
Since the aluminum is stretched while being forged, the density of the structure increases, and high-strength molding becomes possible.
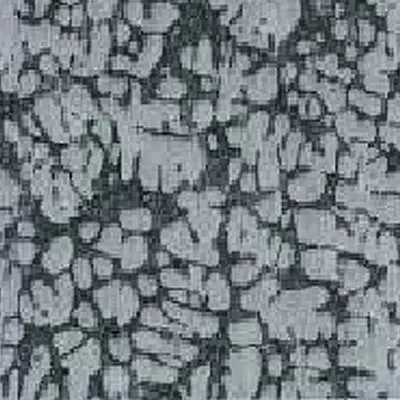
Aluminum structureduring casting
Since it is simply poured into a mold, the density of the aluminum structure is low, which is slightly disadvantageous in terms of strength.